New logistics center facilitates efficient, effective patient care
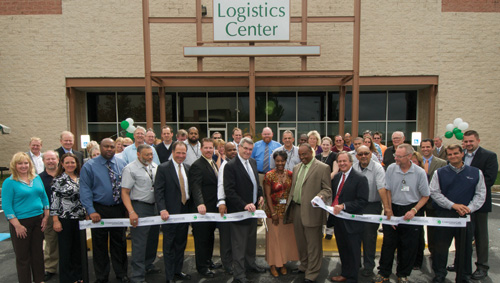
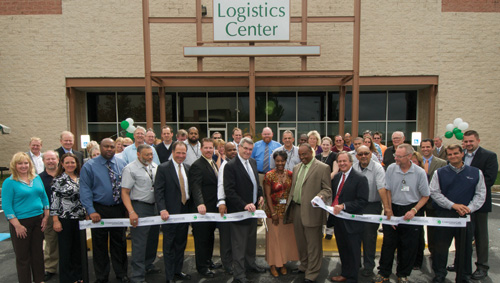
For every action there is a reaction. Thus, as Christiana Care physically expands to take care of the communities we serve, a logistical challenge arises for those responsible for ensuring adequate supplies are on hand when needed.
Christiana Care’s latest reaction to the continued growth of our health system is the opening of a new Logistics Center—a 43,000-square-foot facility in New Castle, Del. Operating six days a week, with 29 full-time employees, the new facility consolidates receiving and distributing of all medical and other supplies into one location.
“Previously, we had a little bit of everything everywhere,” Materiel Management Director Mark McDermott said. “We were using 11,000 square feet downstairs in Christiana Hospital as a warehouse and about 3,000 square feet in Wilmington Hospital, along with smaller storage areas at many other locations. It’s difficult to operate efficiently that way.” McDermott said that the time, energy and truck traffic involved in stocking so many “sub-warehouses” amounted to duplication of effort and inefficient processes.
“The center represents a significant step in the transformation of our supply chain services here at Christiana Care,” said Logistics Manager Dan Hangarasa. “Now, all deliveries come here and then are either sent on for delivery to end users or placed into inventory.” Everything arrives in one place, gets parceled out based on end-user locations and their needs, and then sent on to those locations in customized totes. Nursing units, for example, receive supplies specifc to each unit’s needs.
“This makes the process infinitely simpler than keeping track of numerous shipments, deliveries and trucks servicing multiple drop-off points,” Hangarasa said. Vendors now have their work streamlined as well, through the consolidation of multiple orders into fewer, larger shipments. There is no longer any reason for the same company to make more than one delivery or use more than one driver and truck.
“We use our own vehicles now,” McDermott says, “making 12 to 15 daily round trips from the center to the Christiana Hospital and Surgicenter and six or eight round trips each day to the Wilmington Hospital and Arsht Surgicenter.” As a result, nursing units and clinical departments have supply quantities on hand that are much more balanced to their needs. Space for storage of supplies and time spent organizing and replenishing them is greatly reduced.
“The expansion of the Wilmington Hospital was a key catalyst for the new Logistics Center,” McDermott said. “We had already outgrown the available square footage there.” Previously, nearly 100 items had to be sent from the Christiana Hospital to the Wilmington Hospital every day, simply because there was no space to keep them on-site.
Better disaster preparedness is another important benefit of a centrally located warehouse. Previously, materials were kept in trailers and small storerooms in various locations, but the new Logistics Center, in addition to having the storage capacity for $1.6 million worth of materials — enough to service the whole health system for 18 days—keeps an additional $357,000 on hand in sequestered disaster supplies, which are rotated among overall stock to stay ahead of expiration dates. These supplies are now kept current and can be dispatched quickly to wherever they may be needed in an emergency or disaster situation without imposing undue demand on supplies needed for normal operations.